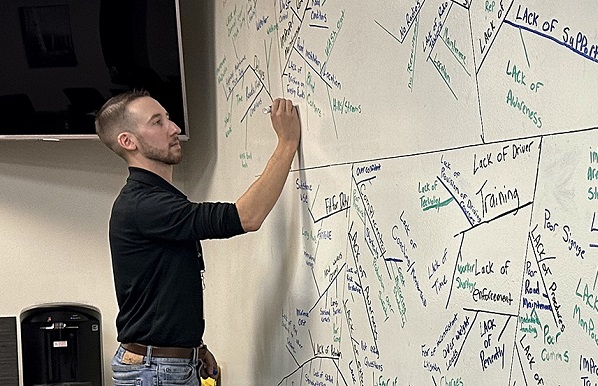
New research reveals key concerns and practical solutions
In March 2024, a volunteer group of industry experts met to assess workplace risks in Ontario’s paper products sector. The group included people from management, labour, government, and not-for-profit organizations. It was led by Konor Poulin, a Health and Safety Representative from Workplace Safety North (WSN).
Stationary machines: A major safety concern
Before the workshop, each participant listed their top health and safety concerns. During the one-day meeting, all 29 identified risks were reviewed. Both labour and management agreed that one of the biggest dangers workers face is the risk of injury from stationary machines used to make, move, pack, or wrap paper products.
Identifying and addressing root causes
“Using the risk assessment method and analyzing their root causes is a very effective way to identify issues before they cause harm,” says Poulin. “This proactive approach helps improve health and safety across the industry.”
A few months after the initial workshop, eight experts met again to pinpoint the main causes of machine-related injuries and come up with solutions. They found that a lack of on-the-job training on how to use the machines was the biggest cause of injuries.
The group created a statement to summarize the issue: “Using stationary machines to produce, move, pack or wrap paper can cause injuries to workers.”
Top causes of machine-related injuries
Here are the top 10 causes of injuries related to machines in the paper products sector (view infographic poster):
- Insufficient hands-on training: Workers often lack hands-on training that fits their learning styles and job needs.
- Focus on speed over safety: A workplace culture that prioritizes productivity can lead to shortcuts, poor maintenance, and ignored safety protocols.
- Lack of proper safety guards: Equipment often lacks proper safety guards due to differing international standards, cost concerns, or lack of reviews.
- Crowded workspaces: Insufficient space leads to congestion and unsafe working conditions.
- Ineffective health and safety program: There’s often a lack of clarity about who is responsible for safety and why it matters.
- Ineffective machine shut down systems: Ineffective lockout-tagout (LOTO) program means procedures are not well-established, and there is a lack of understanding about when and how to use LOTO.
- Inadequate hazard identification program: Many workplaces either do not have or do not follow formal processes to identify hazards. Unsafe practices are often accepted as the norm.
- Training programs are inadequate: Training programs are often rushed or overlooked due to a focus on production over safety, high scheduling demands, lack of recordkeeping, and insufficient oversight.
- Misuse of equipment: Machines are often used incorrectly due to a lack of knowledge or tools, often because of cost constraints.
- Lack of change management: There is often inadequate implementation of process changes, leading to unclear requirements, ineffective communication, and lack of follow up.
Steps to prevent workplace injuries
“The root cause analysis showed several key problems with how workers use stationary machines,” says Poulin. “Experts created a specific list of preventative steps to share with the sector.”
The issues included inadequate training, poor safety culture, lack of machine guarding, crowded workspaces, ineffective health and safety programs, ineffective LOTO procedures, and improper equipment use. Here are some recommended prevention measures:
1. Job-specific and ongoing training
- Provide job-specific training that is regularly reviewed and validated.
- Ensure that training is hands-on, with procedures clearly outlined and reviewed annually.
- Keep detailed records of all training and offer refresher courses regularly.
- Incorporate mentoring and technology-enhanced training methods, such as video instructions and interactive components.
2. Commitment to safety over productivity
- Establish a safety-first culture, with a committed schedule for safety meetings and maintenance.
- Train supervisors and ensure effective communication between all levels of staff.
- Conduct regular safety talks, surveys, and inspections to reinforce safety values.
3. Regular machine audits
- Develop and maintain a safety audit system for all machines, including regular checks and documentation.
- Involve workers, supervisors, and safety committees in the audit process.
- Introduce new technology and guarding styles to enhance machine safety.
4. Maintaining an orderly environment
- Implement organizational methods like 5S to keep workspaces free of clutter.
- Regularly inspect work areas for congestion and maintain clear, safe spaces.
- Work with sales and production teams to manage inventory and reduce congestion.
5. Effective lockout-tagout procedures
- Ensure that all equipment has accessible LOTO boards, with regular audits to confirm compliance.
- Provide ongoing training and validation to ensure all energy sources are locked out correctly.
- Implement a clear, consistent LOTO program that meets safety standards.
6. Comprehensive hazard identification
- Train workers on how to identify hazards and implement a site-wide risk assessment.
- Maintain a hazard reporting and mitigation program that is actively monitored and documented.
Implementing safety solutions
By addressing these root causes and implementing these preventative measures, the paper products sector in Ontario can create a safer work environment for all its workers.
For more information, visit the Workplace Safety North website or contact your local WSN Health and Safety Specialist.
Related
Technical Paper: Ontario Paper Products Sector Root Cause Analysis Workshop Results
Poster: Top 10 root causes of injuries from equipment in paper products sector
Article: Ontario paper products sector unwraps top 10 health and safety risks
Poster: Top 10 Health and Safety Risks in Paper Products Sector
Paper, printing and converting sector risks assessments and root cause analyses including pulp and paper, corrugating, and paper products sectors
Free paper, printing, and converting health and safety resources, including guidelines, safety talks, posters, and more