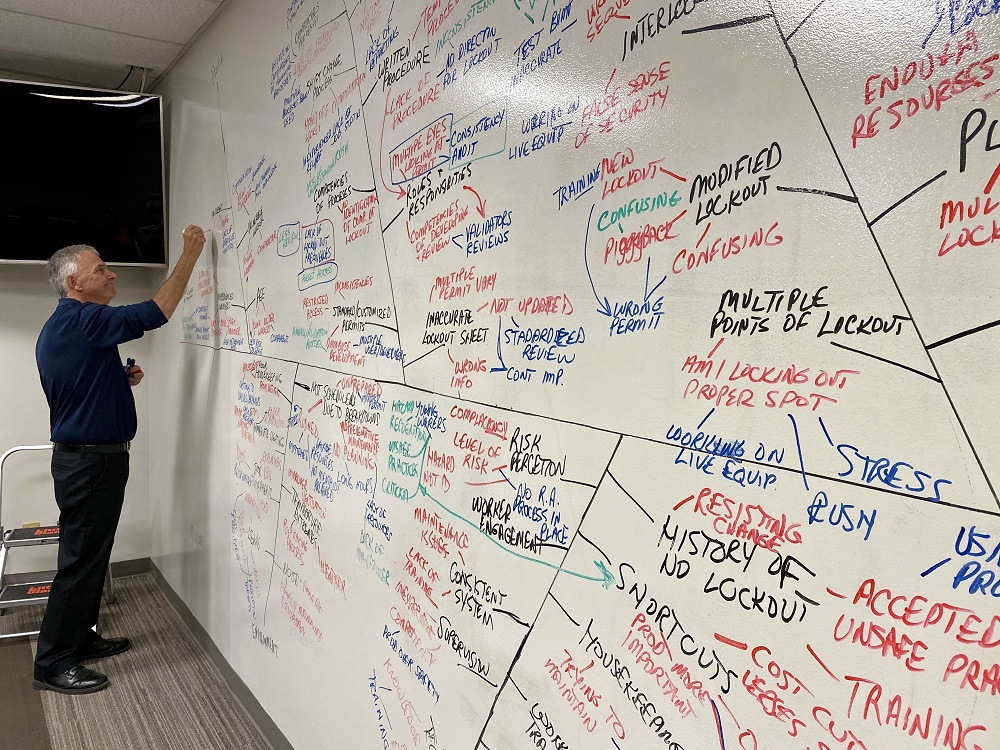
Jerry Traer, Program-Training Specialist at Workplace Safety North, in North Bay on September 30, 2020, helping facilitate a virtual root cause analysis with Ontario pulp and paper sector subject matter experts to determine the root cause of the top risk, the inadequate or improper lock out of machinery.
Groundbreaking analysis gathers industry-generated predictive information to better prevent workplace injuries and illnesses
Ontario workplaces may be about to get safer thanks to a risk-based analysis developed by the Ministry of Labour Training and Skills Development, and facilitated by health and safety associations like Workplace Safety North.
The success of this approach has provincial health and safety associations like Workplace Safety North expanding their capacity to conduct industry workshops on risk assessment and root cause analysis.
“The risk assessments and root cause analyses are working; it’s giving us the kind of information we need, in terms of enhancing predictive capabilities and coming up with interventions that are targeted, and moving away from the whole notion of a one-size-fits-all solution to hazards,” says Sujoy Dey, Ph.D., Corporate Risk Officer at the Ministry of Labour, Training and Skills Development. Dey specializes in the management of risk and decision analysis under conditions of high business variability and operational uncertainties.
Risk-based analysis is for everybody in the health and safety world
Conducting industry-specific risk assessments and digging further to find out the root causes of those risks has given health and safety associations much clearer insight into what keeps workers and supervisors up at night in terms of top risks in the workplace.
“Lagging indicators are just one part of the entire predictive aspect or story, but leading indicators is what will make it happen in terms of prevention,” says Dey. “Because in the end, it’s all about prevention.”
“That’s the main theme. And of course, we are here to assist, help support industries in getting those injury and illness rates down. Risk-based analysis is for everybody in the health and safety world.
The ability to facilitate these assessments and analyses has become a capacity issue for the province, and new train-the-trainer training was developed by the Ministry and piloted this year.
New workshop training launched in Ontario
With the help of Tom Welton, Director of Prevention Services and Education Programs and his team at Workplace Safety North, the Ministry launched new virtual ‘train-the-trainer’ training for the health and safety associations.
Based on best practice risk assessment and root cause analysis that were led for various sectors, the training teaches health and safety specialists how to facilitate both a risk assessment and a root cause analysis with industry subject matter experts.
Sector risk assessment workshops require the gathering of a volunteer group of diverse industry subject matter experts – including workers, supervisors, and employers from large and small companies – who submit their top health and safety concerns in advance of the workshop. During the workshop, the submitted concerns are discussed and ranked by the group using an anonymous electronic voting mechanism.
From there a list of top ten risks for the sector is created. For example, in the sawmill sector, substance use was identified as the top hazard – something that is not tracked by WSIB.
The next step is to get at the root cause of each identified risk. Currently, each sector is focused on just one of the top risks, and the industry would like to build capacity to be able to work their way through the list of the top ten risks.
Root cause analysis workshops require the same gathering of diverse industry subject matter experts. It’s important to note that both worker and supervisor points of view are included. The group discusses and discovers the root causes of the risk in the workplace. From there, the group develops critical controls and specific activities that can be put in place to help mitigate the risk.
Timeline of Ontario industry sector risk assessments and root cause analysis
A risk assessment is a formal risk ranking of health and safety hazards in a specific industry sector, as identified by the workers, supervisors, and employers in that sector.
After the top ten risks are identified, the next step is a root cause analysis, starting with the top risk.
Industry response to risk-based analysis has been strong and sector advisory committees have encouraged the government and health and safety associations to build capacity in order to do more workshops.
“When we talk about predictive capability, we are talking what everybody really wants and has a tough time getting to: leading indicators,” notes Dey.
“So the risk assessment method, followed by the root cause analysis workshops, provide a lot of opportunity for analysts to work on leading indicators; the ability to lay that foundation for metrics that were never there. That is the ‘why’ for risk-based analysis, and for launching this training that will allow us to build capacity to gather these new metrics.
“Just to summarize: number one is the capacity; the ability to do more, and the second is, of course, to do more and have a robust predictability through leading indicators.”
Both Dey and Welton were approached by industry advisory board members who wanted to continue analysis of top risks in their sectors. The requests led to a discussion about how to build capacity.
“For example, working at heights might be different for construction versus working at heights in underground mining to greenhouses to surface mining. So, it’s the ability to have that targeted predictive capability.
New training piloted in August for first virtual analysis in September
In November 2019, WSN facilitated a risk assessment workshop for the pulp and paper sector. The follow-up root cause analysis workshop planned for May had to be postponed due to COVID-19. With the new training, WSN staff was able to facilitate it virtually on September 30 and October 1. With the pilot completed, WSN will develop a strategy for priority sectors.
“Since WSN was on top of things right from the get-go,” says Dey. “I appreciate the fact that they decided to work with me on innovating on how to try and recreate the successes of a face-to-face workshop, and how can we translate that into a virtual experience and they’ve been very supportive.”
Other provinces have shown interest in the risk-based approach. In the past few years, results of Ontario's risk-based analyses have been presented to government and health and safety organizations in British Columbia and Alberta. The material was translated into French and provided to the Quebec mining sector.
Integrating risk-based analysis into provincial occupational health and safety strategy
Risk-based analysis with its predictive perspective is a new direction in the Ontario occupational health and safety strategy.
“It’s going to be the way things work in terms of integration into the new occupational health and safety strategy, it’s going to be very interesting,” says Dey.
Celebrating engagement with the sector
The workshops focus on diversity of participants and ample participation through discussion and anonymous voting. While the risk-based analysis tool is important, the emphasis is on method – ensuring all perspectives are respectfully heard and noted.
“The program’s success comes from how we celebrate the engagement we have with the sector – both on the worker side as well as the employer side,” says Dey. “And not just industry sectors but the system – be it our frontline inspectors or sectors that cross boundaries in terms of regulations. For example, the trucking sector, you have both provincial as well as the federal folks, then you have research.
“The risk assessment and root cause analysis workshops definitely celebrate that engagement. To be a little more clear: The success of these workshops – I always say it’s not the choice or the tool that you select to use for the risk assessment or root cause analysis – it’s basically how you go about doing it."
Training available to all health and safety associations
The new virtual training aims to expand the province’s ability to do many more risk assessments and root cause analyses for industry. This will provide both the industry and employers increased access to grass roots insights that focus on leading indicators.
“This training is definitely for the health and safety associations [HSAs],” says Dey. “Once we work with HSAs, we’ll have good feedback and then we can fine-tune the training and probably develop a manual that people can use in the future. So, the focus right now is just the HSAs in order to work on the capacity that was needed to conduct all these workshops across all the sectors.”
“Due to the need and request from stakeholders – the member firms of Ontario health and safety associations – we are working hard to meet their requests. We can see risk-based analysis is resonating extremely well with Ontario sectors and the health and safety world.”
Related
Sawmill sector
Substance abuse top health and safety risk at sawmills
Infographic: Top 10 Health and Safety Risks in Sawmills
Industry experts analyze causes of substance use on the job
Infographic: Top 10 Causes of Substance Use in Ontario Sawmills
Technical Paper: Root cause analysis report of substance use in Ontario sawmills
Logging sector
Distracted driving top health and safety risk for logging operations
Infographic: Top 10 Health and Safety Risks in Logging Operations
Industry experts analyze causes of distracted driving on the job
Infographic: Top 10 Causes of Distracted Driving for Logging Operations
Technical Paper: Root cause analysis of distracted driving in Ontario logging operations
Pulp and paper sector
Deficient lock out of machinery top health and safety risk in pulp and paper sector
Infographic: Top 10 Health and Safety Risks in Pulp and Paper Sector
Industry experts analyze causes of deficient lockout of machinery
Infographic: Top 10 root causes of deficient lockout in Ontario pulp and paper operations
Mining sector
New Ontario guideline for mining workplace risk assessments
Worker contact with motor vehicles top health and safety risk for mining operations